Smart Optimization: Advanced Dashboard for Soybean Oil Production at Ragasa
This project was conducted for Ragasa, a company dedicated to the milling of oilseeds, within the agro-industrial sector. The main objective was to develop a dashboard that implemented analytical capabilities and artificial intelligence models at key points in the soybean oil production process. The dashboard needed to cover the stages of grain unloading, transport, and storage, as well as oil extraction and refining. By integrating control panels, logs, real-time analysis, and predictive algorithms into a single platform, the aim was to facilitate data-driven decision-making that would increase efficiency and productivity.
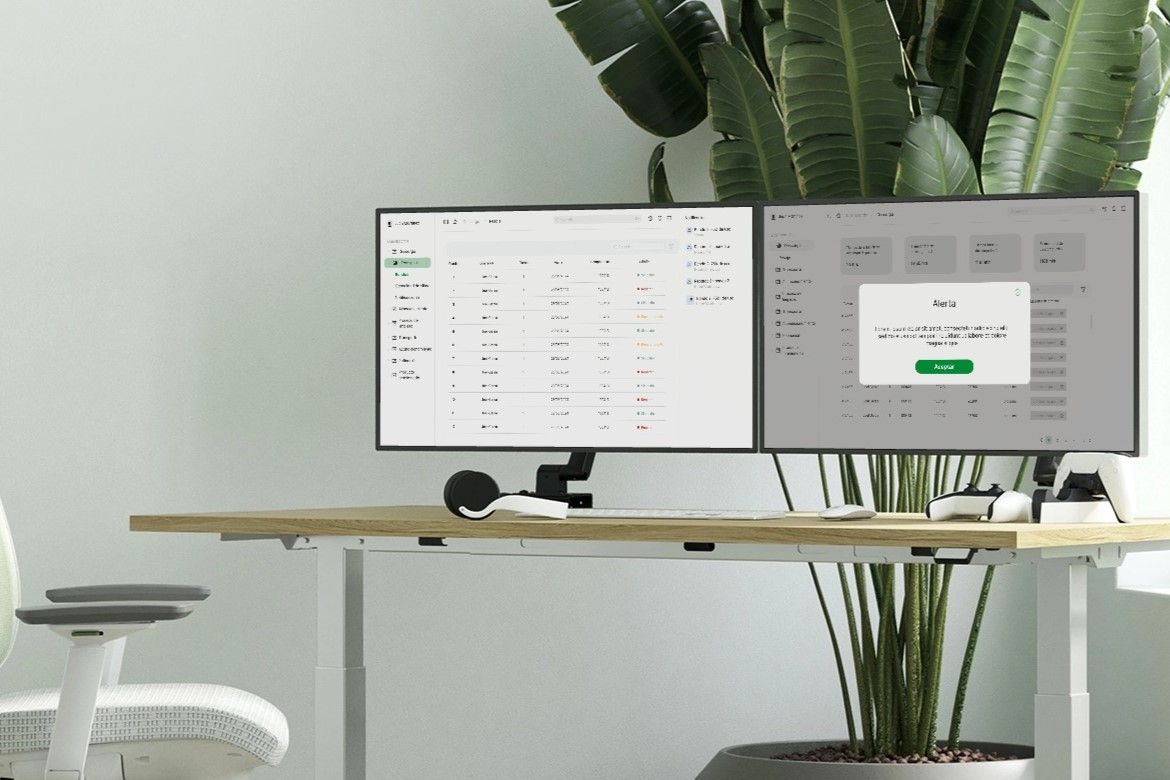
Detailed Project Development
Challenges and Objectives
The primary challenge of the project was to integrate various data sources and processes into a coherent and user-friendly platform. Additionally, it was crucial to develop artificial intelligence models that could learn and adapt to Ragasa's specific data. The objective was to create a tool that not only visualized data but also offered predictive analysis to anticipate problems and optimize production.
Design Process
The design process began with an extensive research phase. Discovery workshops were conducted using Miro with the Design Thinking methodology, involving product owners and end-users to identify their needs and challenges. This phase included interviews and brainstorming sessions to deeply understand the operational processes and user expectations.
Subsequently, low-fidelity wireframes were developed in Figma to outline the basic structure and functionality of the dashboard. These wireframes were iterated continuously based on stakeholder feedback, ensuring they aligned with user requirements. Once the low-fidelity wireframes were approved, high-fidelity wireframes were created, detailing the visual design, including the implementation of a design system with specific buttons, icons, and cards for the dashboard.
The next step was prototyping, where interactive prototypes were developed in Figma. These prototypes were tested with end-users in remote usability sessions, allowing us to identify and resolve usability issues before the final implementation.
Key Features
The dashboard included several key features, such as customized control panels for different stages of the production process, logs to record critical events, real-time analysis to monitor operational performance, and predictive algorithms that helped anticipate problems and optimize production. Integrating these features into a unified platform allowed users to easily access relevant information and make informed decisions quickly and efficiently.
Project Outcomes
The project resulted in a significant improvement in Ragasa's operational efficiency. The dashboard allowed operators and managers to monitor and control the production process more effectively, reducing downtime and associated production costs. Additionally, the predictive algorithms helped anticipate and resolve issues before they impacted production, resulting in improved product quality.
Learnings
Several new skills were acquired during the project, such as advanced use of Miro for remote collaboration and implementing a comprehensive design system in Figma. Understanding the integration of artificial intelligence models into operational dashboards was also crucial for the project's success. Effective remote collaboration was another important learning, highlighting the importance of clear communication and the right collaboration tools.
Conclusion
This project was a valuable experience demonstrating the positive impact of analytical tools and artificial intelligence models on industrial production. Initial challenges, such as integrating multiple data sources and developing effective predictive models, were overcome through careful research and design. The learnings obtained, including handling remote collaboration tools and implementing design systems, were significant. The project's success lies in its ability to improve Ragasa's efficiency and productivity, providing a robust and user-friendly solution that can continue to evolve over time.