Dashboard for Defect Detection in Automotive Parts
Develop a dashboard to detect defects in automotive parts as they move along the production line. Operators would mark errors to help train the AI, improving the dashboard’s accuracy over time. This project aimed to enhance quality control and reduce defective parts in the final product.
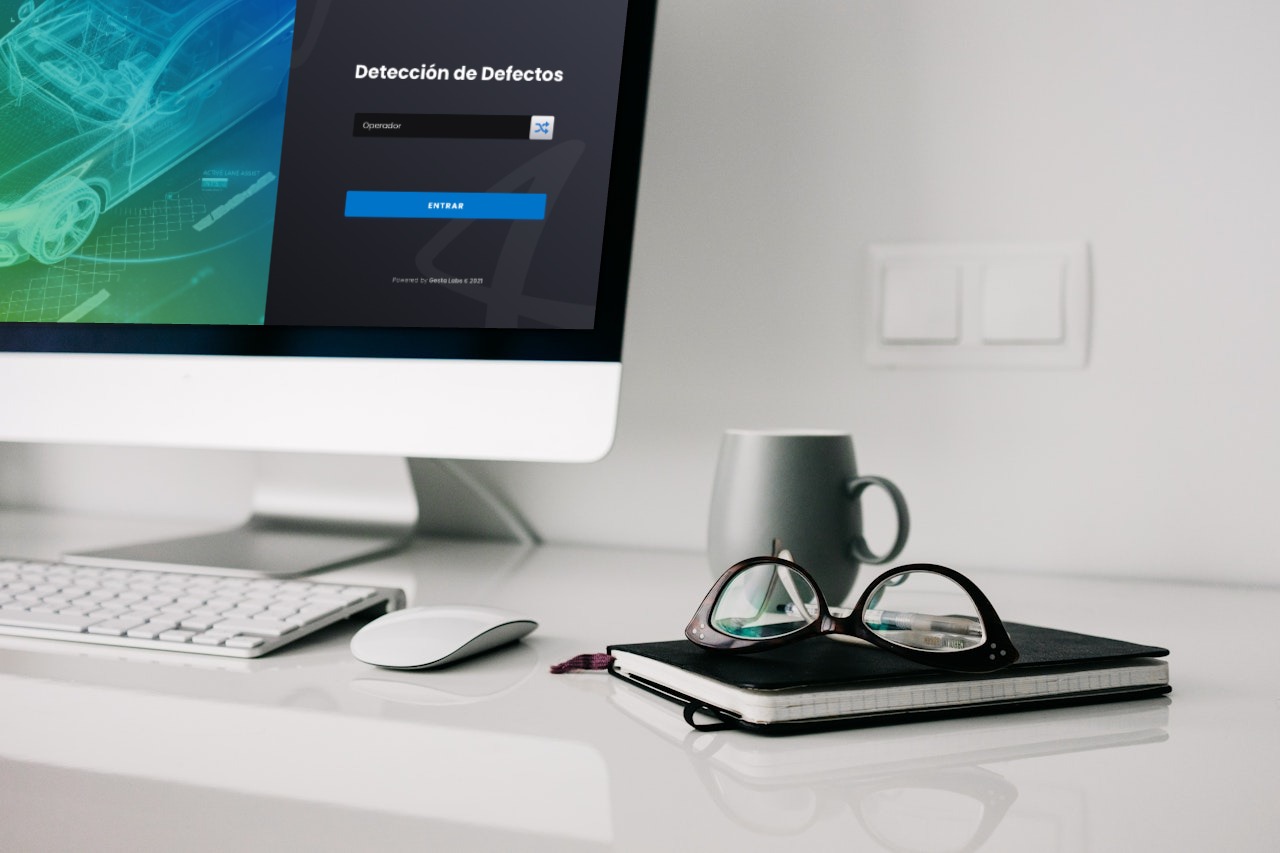
Client: Nemak
Industry: Automotive
Project Duration: 20 weeks
Objective
The primary goal of this project was to develop a dashboard that could detect potential defects in automotive parts as they move along the production lines. If a piece was incorrectly marked, the operator would highlight the error with a marker, helping to train the AI and improve the dashboard’s performance over time.
Collaboration
This project was executed entirely remotely, necessitating efficient communication and collaboration tools. Slack and Google Teams were utilized for regular meetings and updates, ensuring continuous improvement of the user experience.
Tools and Platforms
- Miro: Used for discovery workshops with product owners and end-users (operators).
- Adobe XD: Employed for developing low and high-fidelity wireframes and prototypes, as well as implementing the design system.
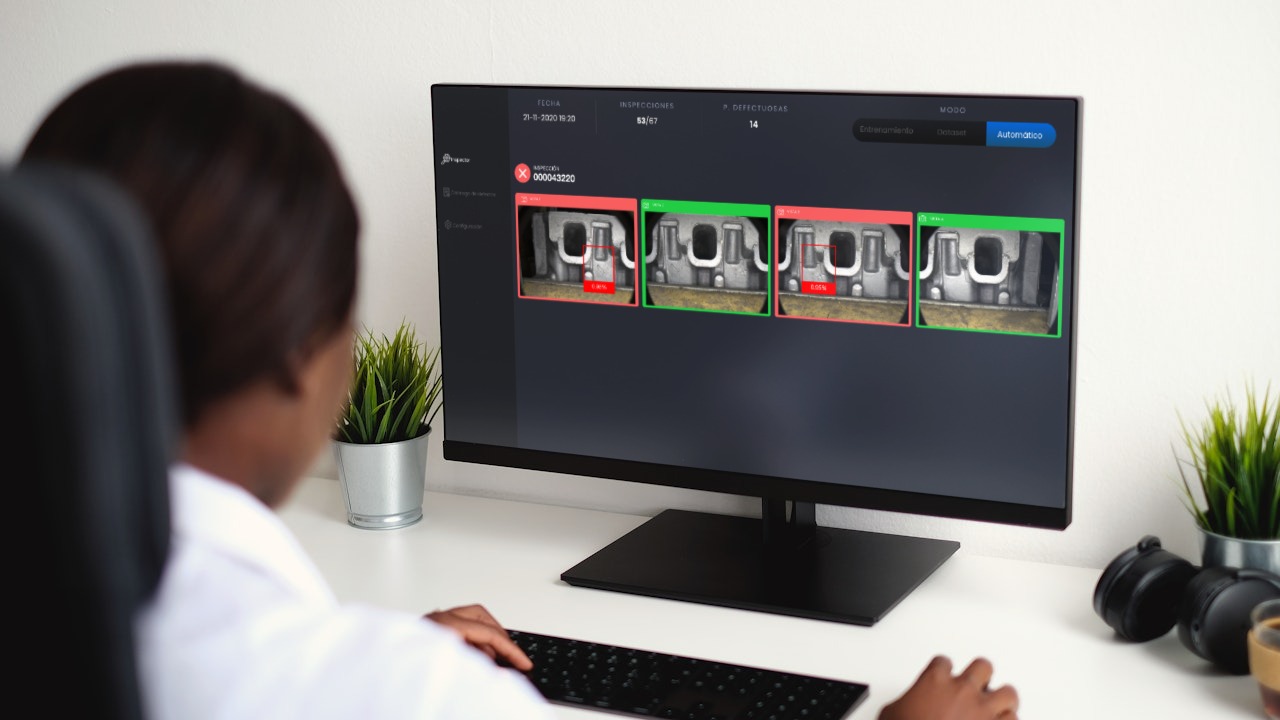
Design Process
Research and Discovery
Stakeholder Interviews: Conducted interviews with product owners and end-users to understand their needs and challenges.
Competitive Analysis: Analyzed existing solutions for defect detection dashboards in the automotive sector.
User Journey Mapping: Created detailed user journey maps to identify pain points and areas for improvement.
Wireframing
Low-Fidelity Wireframes: Developed initial sketches and low-fidelity wireframes in Adobe XD to outline the basic structure and functionality of the dashboard.
Feedback and Iteration: Gathered feedback from stakeholders and iterated on the designs to address any concerns and incorporate suggestions.
Prototyping
High-Fidelity Prototypes: Created detailed, interactive prototypes to simulate the final user experience.
Usability Testing: Conducted remote usability testing sessions with operators to ensure the interface was intuitive and met their needs.
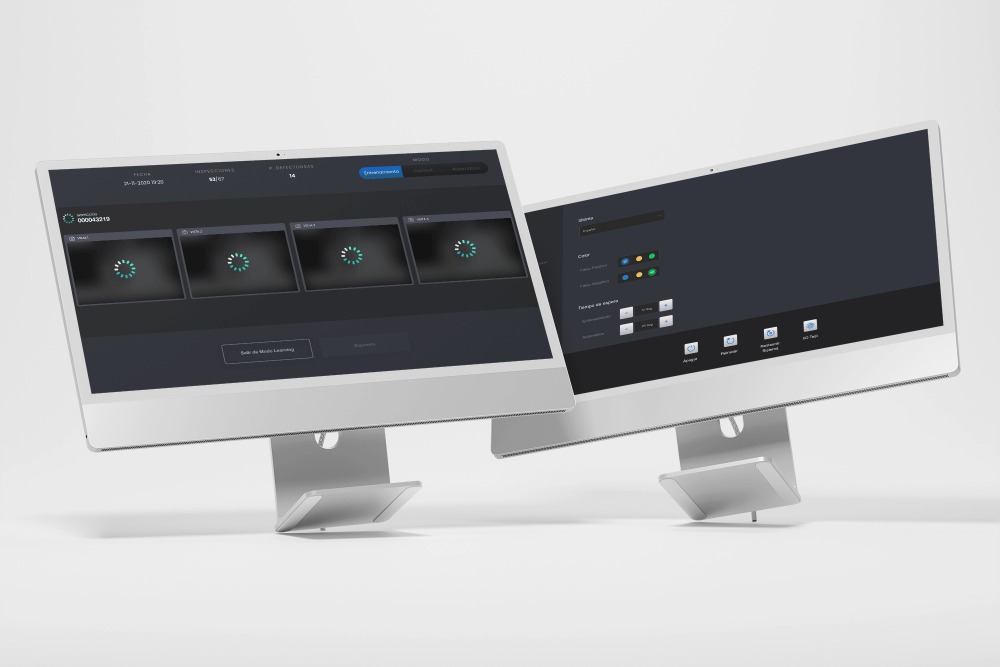
Visual Design
Design System Implementation: Established a comprehensive design system to maintain consistency across the dashboard.
Visual Enhancements: Applied visual design principles to enhance the aesthetic appeal and usability of the dashboard.
Key Features
- Real-Time Defect Detection: The dashboard provides real-time updates on detected defects, allowing operators to take immediate action.
- AI Training Integration: Operators can mark incorrect detections, feeding this data back to the AI to improve its accuracy over time.
- User-Friendly Interface: The dashboard is designed with operators in mind, ensuring ease of use and quick access to critical information.
- Customizable Alerts: Users can set up customizable alerts for different types of defects, improving response times.
Project Outcome
The dashboard successfully streamlined the defect detection process, significantly reducing the number of defective parts reaching the end of the production line. The AI training integration led to continuous improvement in detection accuracy, resulting in higher overall product quality.
Learnings
- New Tools: Gained proficiency in using Miro for remote collaboration and discovery workshops.
- AI Integration: Enhanced understanding of integrating AI feedback mechanisms into user interfaces.
- Remote Collaboration: Improved skills in managing remote projects and ensuring effective communication and collaboration through digital platforms.
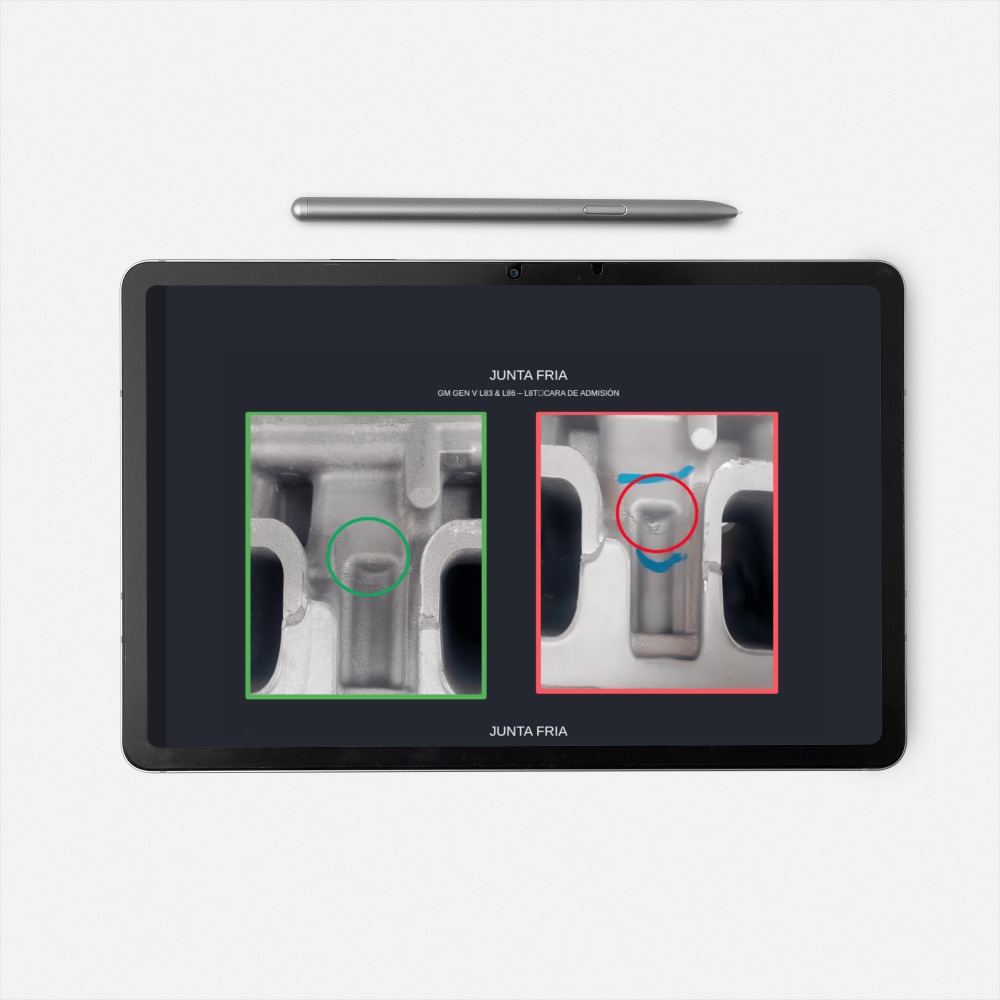
Conclusion
This project was a valuable experience in developing a sophisticated tool for the automotive industry, combining cutting-edge technology with user-centered design. The main challenges involved ensuring the AI's accuracy and creating an intuitive interface for operators. By overcoming these challenges, the project not only improved the defect detection process but also provided insights into the potential of AI in enhancing industrial operations.